ReCyCONtrol
ReCyCONtrol - Self-learning control techniques for the production of robust resource protection concretes
Resource-efficient circular economy - construction and mineral material cycles (ReMin)
The closing of the building material cycle in the construction industry, and in particular in concrete construction, is extremely hindered by the pronounced scattering of the material properties of recycled materials. The RecyCONtrol project addresses this issue by developing innovative sensor technologies and self-learning control processes for concrete production. Using these systems, the fluctuations in the recyclates are to be recorded in real time for each mixer batch during concrete production and their effect on the fresh concrete properties controlled by dosing an additive system developed in the proposed project.
The project is being funded as part of the "Resource-efficient circular economy - construction and mineral material cycles (ReMin)" funding measure. "ReMin" is part of the BMBF research concept "Resource-efficient circular economy" and is aimed at resource-efficient construction and the expanded use of mineral secondary raw materials from construction waste, slag, ash and mining residues.
Gap in the circular economy for building materials
Approximately 8 percent of global anthropogenic greenhouse gas emissions (primarily CO2) are released during cement production alone. In Germany, the construction industry also accounts for 560 million tons of annual raw material consumption. This corresponds to around 90 percent of the consumption of mineral resources. While the construction industry in Germany produces around 213 million tons of waste every year (≈ 57 percent of the total amount of waste), only around 25 percent (56 million tons of recyclable construction waste) of this waste can be recycled. Instead, the handling of mineral resources in the construction industry is characterized by down-cycling rather than genuine recycling.
Previously uncontrollable material fluctuations
There are many reasons for the gap in the building materials cycle, but one major cause can be identified: Increased fluctuations in the material properties of the recyclates have a negative impact on the robustness and quality of the new concretes produced from them. Although the negative effects of these fluctuations in material properties can be compensated for by a significant increase in cement content (up to 20 percent in some cases), this is neither economically nor ecologically justifiable. The use of recycled materials, which is desirable for environmental reasons, is therefore in direct competition with the required reduction of greenhouse gas emissions in concrete production. Another approach to counteracting these fluctuations is to separate disadvantageous components by screening. However, the quality of the separated residual materials is then usually so low that they are no longer suitable even for down-cycling and have to be disposed of in landfills. This approach is therefore also not expedient.
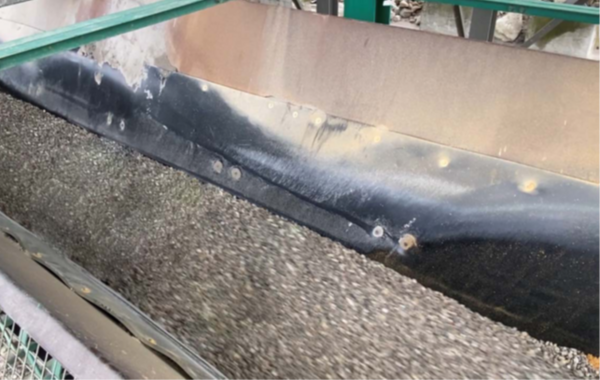
Key technology "Concrete production 4.0"
A key to significantly increasing the use of concrete recyclates lies in the development of technologies that make it possible to continuously record and control the influence of fluctuations in these substances on the end product without negatively affecting the economic efficiency and environmental balance of the end product. In order to raise concrete production to the Industry 4.0 standard in the future, automated, self-learning process monitoring, control and regulation methods are required, which use non-contact measuring systems to detect the detrimental material fluctuations of the concrete raw materials and, based on this, adjust the properties of the end product concrete by adding specially adapted additives during the mixing process.
Computer vision in concrete construction
As part of the ReCyCONtrol project, this type of technology is being developed in a targeted manner. The core element of the development is to record the flow behavior of the concrete during the mixing process using so-called computer vision methods and to evaluate it with regard to the existing fresh concrete properties. Based on this measurement technology, it is possible to quantify the influence of changes in the concrete composition directly in the mixer and to control the mix by adding new additives on the basis of the data obtained in this way. Thanks to continuous data acquisition, the control software of the mixing plant can be designed to be self-learning. This means that the system itself learns how to control the mixture most effectively by changing the composition. According to the applicants, this can significantly increase resource efficiency in the production of concrete.
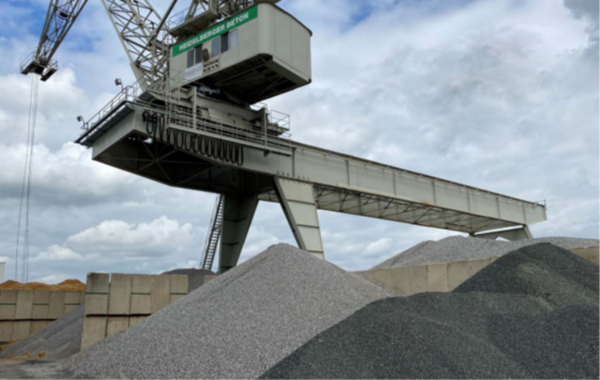
Funding measure
Resource-efficient circular economy - construction and mineral material cycles (ReMin)
Project title
ReCyCONtrol - Self-learning control technologies for the automated production of robust resource protection concretes - key to the comprehensive recycling of mineral material flows
Duration
01.05.2021-31.04.2024
Funding reference
033R260
Funding volume of the consortium
2,255,381 euros
Contact
Prof. Michael Haist, Dr. Dries Beyer
Leibniz Universität Hannover | Institute for Building Materials
Appelstraße 9A | 30167 Hannover
Phone: 0511 762-3258
Email: d.beyer@baustoff.uni-hannover.de
Project partners
Master Builders Solutions Deutschland GmbH; Heidelberger Beton GmbH; Pemat Mischtechnik GmbH; Bikotronic GmbH; alcemy GmbH || Associated partners: Federal Waterways Engineering and Research Institute; Moß Abbruch-Erdbau-Recycling GmbH & Co KG
Internet
recycontrol.uni-hannover.de
Data sheet
Download data sheet